What is “Reverse Logistics” and How Can You Benefit From It?
“Reverse Logistics”
Returns management is a key to e-commerce success. Consumers returned around $400 billion in 2020, and reverse logistics can help you track products from the point of return by the customer and manage where they end up. The cost of reverse logistics might seem prohibitive at first glance, but the money you save is more than enough for the initial cost.
Furthermore, a reverse logistics provider helps retailers manage returns and processing costs. The expenses of $106 million for every billion in sales can be saved by outsourcing the job to a 3PL company that specializes in this service. These companies have been around for decades, so they know how to manage their resources more effectively than traditional retail giants do on their own.
“Reverse Logistics” is a new concept in the shipping industry. It involves companies taking back products from consumers and refurbishing them for resale rather than sending them to landfills. In many cases, this process can be costly, time-consuming, and difficult due to damaged or unusable items that need repackaging before being sent out again – not just because of the costs associated with shipping but also because of what it takes to assess returned goods for damage on customers’ behalf.
In the past, companies were unaware of what it would take to get their products back from consumers and into a re-saleable condition. Reverse logistics is a cost-saving solution that allows for better product utilization while also minimizing expenses on store shelves.
In the world of marketing, every company will eventually experience a decline in its revenue. In retail, it’s usually due to returns and discounts from customers that they don’t make money on. Reverse logistics is an effective solution for retailers who want to reduce these losses by reducing inventory levels and improving customer retention rates with better quality products, and increasing the sales growth.
Reverse logistic companies typically focus on understanding what causes return activity so that they can improve processes around the collection, processing, and distribution.
Reverse logistic companies also need to be able to analyze their data so that they can make informed decisions regarding the future of how they operate.
Reverse logistics helps businesses get their returned products back into the supply chain. It is a process that automates managing every stage of the returns lifecycle and identifies where to return items that will generate high-cost recovery.
Reverse logistics is a process that makes it easier for customers to return items. It starts with the customer, who can start returning their products at any time they want. Machine learning analyzes product demand and sales rules, which allows this system to be tailored according to the needs of your business or retail store.
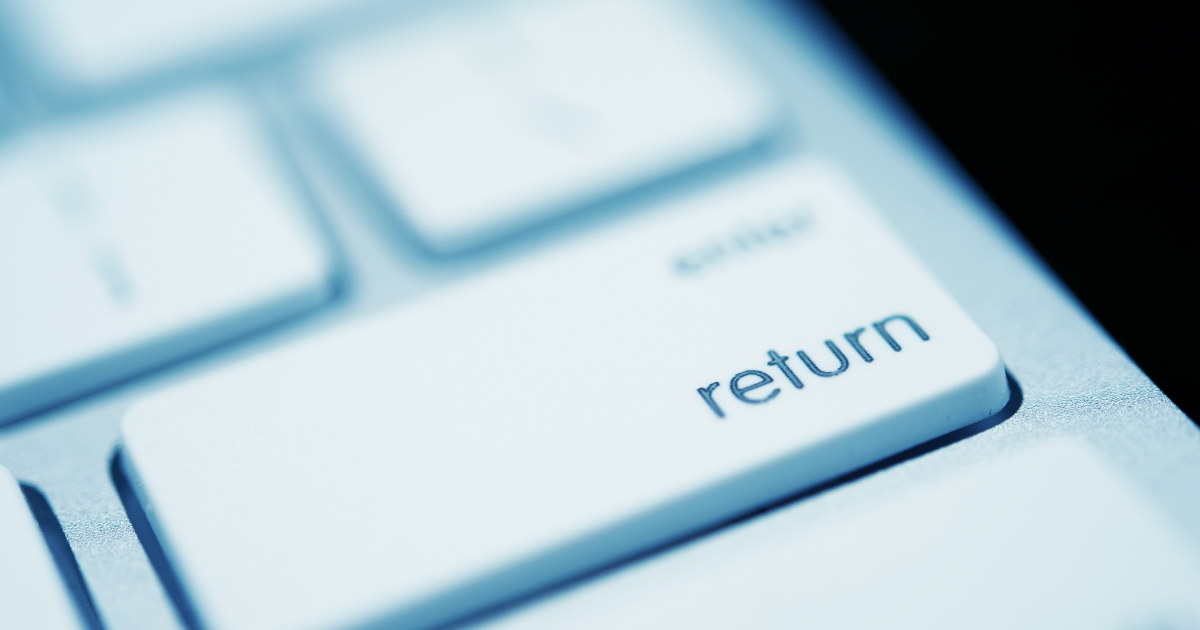
What is reverse logistics?
Reverse logistics is any part of the reuse of products and materials in a supply chain. When an item is not sold, it may be sent back to the manufacturer or distributor for reuse or recycling. This process allows companies to avoid wasting both money and natural resources by avoiding throwing away unsold items that would otherwise go into landfills.
Retailers often consider a product’s supply chain to be complete when it leaves their hands, but there are ways to re-enter the supply chain in order to increase sales.
Reverse logistics is the process of moving goods from their typical final destination for the purpose of capturing value. Reverse logistics provides retailers with a means of recapturing some of that value. The retailer typically takes back products and materials in order to be repaired or recycled, which differs depending on the type and size company it is servicing.
Reverse logistics is the management and sale of surpluses, which can be done in different ways. A reverse supply chain allows for product returns and management of their resale. It has similarities to traditional logistics as it also includes remanufacturing or refurbishing products that no longer have a market value. Still, not all reverse logistics companies agree with this definition.
A reverse logistics strategy can be applied in many scenarios, including when companies are looking to increase their profits. Reverse logistics is the process of planning, implementing, and controlling the efficient flow of raw materials from point-of-origin to point-of-consumption so you can recapture value or properly dispose of them. To implement a successful reverse logistics strategy, companies have to plan for it upfront by creating detailed plans that include what they’ll do with different types of inventory at each stage along its life cycle.
Reverse logistics is the act of taking finished products that are no longer needed and returning them to their original source. This process can be done in many different ways, like producing new goods using used materials or selling unwanted inventory for profit.
The benefits of reverse logistics include reducing waste costs, promoting sustainability by saving resources, providing a more competitive price point with higher margins than traditional supply chains would allow, and creating an attractive customer experience with less packaging material than before–allowing you to create a competitive advantage.
Reverse logistics is a cost-effective and frugal strategy that leads to higher margins, creates an attractive customer experience with less packaging material than before, and provides a more sustainable model for businesses.
Different types of reverse logistics
Reverse logistics is the process of turning waste and returns into usable products. It can be divided into two types: planned and on-demand. Planned reverse logistics includes remanufacturing, refurbishing, packaging, unsold goods, and end-of-life delivery failure rentals & leasing repairs & maintenance. On-demand reverse logistics includes returns, returns avoidance, and remanufacturing for sale or lease back to customers.
Though it may sound like a lot of work, reverse logistics can be highly beneficial to both the business and its customers. For example, on-demand returns allow businesses to more efficiently identify defective products before they are sold to customers. Furthermore, planned reverse logistics can be used by companies in order to help reduce costs and avoid future expenses that come with wasted materials.
Reverse logistics is a process in which the owner of an item disposes of it and then cleans up after themselves. While some products can be inspected and repaired for resale, other items will need to go through a different route, such as liquidation or disposal.
Reverse logistics is the process of remanufacturing or refurbishing. There are two types: returns management and either remanufacturing or refurbishment.
Planned reverse logistics
Reverse logistics is a business strategy that companies use to increase their revenues. Companies that have reverse logistics processes are doing better than those that do not. There is an increasing number of businesses adopting this model in the fashion and furniture industry.
Reverse logistics systems are divided into planned and on-demand. Companies use their return policies to differentiate themselves from the competition, which is a major benefit of reverse logistics. Additionally, companies can reduce costs by using their own return system as well as providing unique product data that may help them correct existing issues.
The reverse logistics process collects data about product defaults and lifespans, which can be used to assess customer satisfaction. Common product defaults are broken down into groups that range from the use of defective products to empty boxes for returned items.
On-demand reverse logistics
“On-demand reverse logistics challenges the standard logistics model of businesses.” In this model, a manufacturer would produce goods and then use 3rd party logistics companies to deliver those goods as quickly as possible. This is seen as an alternative to the current supply chain management system that focuses on reducing costs by centralizing distribution in one location because it can be both more complex and difficult for businesses.
Reverse logistics systems are planned or on-demand, which allows them to remain flexible with their manufacturing process while also meeting customer demands.
Today, there are two types of reverse logistics: planned and on-demand. A company’s reverse logistics process is managed by a separate team with oversight from the CEO to ensure that it remains effective.
The retail industry is under pressure due to the advent of e-commerce and customers’ expectation for easy returns. The brick and mortar retail industry have a return rate of 30%, according to their own statistics, which means that every time an item is purchased online, it will have a significant chance of being returned to where it was bought from. In 2018 alone, global retailers are estimated at making $650 million in just returns, but globally the waste management and recycling industries are worth over 300 billion dollars.
On-demand reverse logistics is a system that allows businesses to take back and repair, refurbish or recycle their old devices. It has been proven to reduce the cost of managing returned products as well as lowering environmental impact by recycling more electronics.
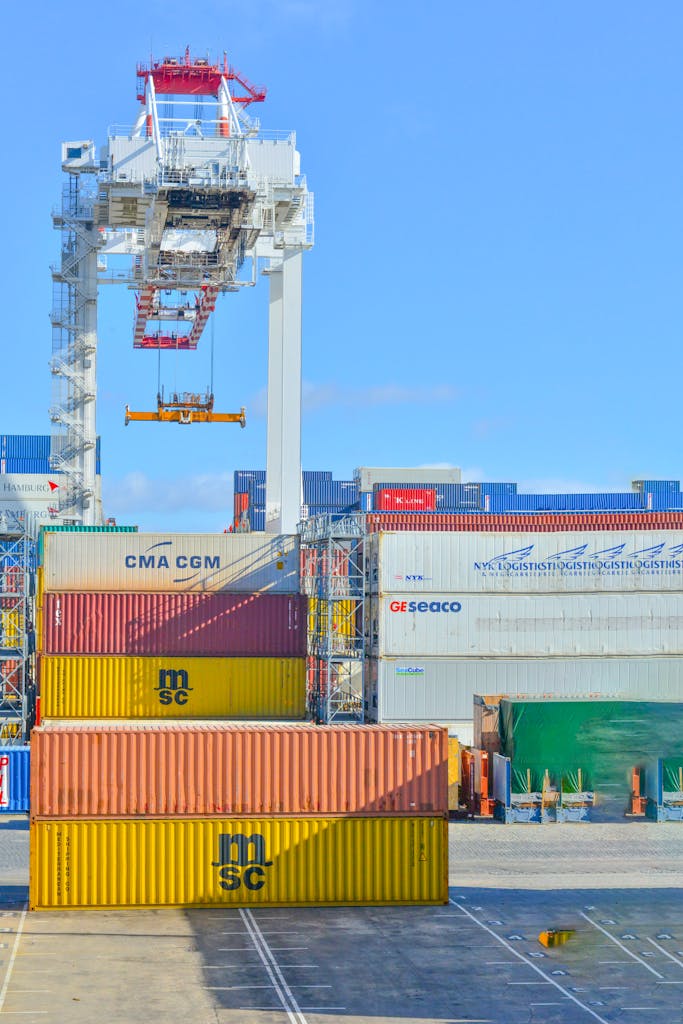
How to manage reverse logistics
Reverse logistics is a supply chain management practice that’s been around for decades. The term “reverse logistics” refers to the process of returning goods from one point in a company’s supply chain while keeping them or recycling them. Reverse logistics can help companies by minimizing challenges and maximizing efficiency, but it also requires an advanced set of capabilities specific to returns and reverse logistics.
The reverse logistics process is a complex one with many moving parts, but if managed correctly, it can be used to increase the return of goods for profit. Successful businesses need a system that includes two key elements: measurement and assessment.
To make the most of your business’s reverse logistics program, you must first understand what those definitions mean as well as how they work together in practice. These tips will help guide you through creating an effective system tailored specifically to your company’s needs.
Increase drop density by adding on-demand returns
Reverse logistics is the last step of regular deliveries. It can be used to increase drop density by adding on-demand returns, but only if the reverse logistics software has enough functionality and drivers can add reverse logistics stops ad hoc.
Reverse logistics is the process of managing returns and ensuring that they are handled efficiently. This allows companies to increase their drop density, which would help them grow.
Use a driver app to manage failed delivery attempts, damaged goods, and compliance
Reverse logistics is the process of managing failed delivery attempts, damaged goods, and compliance. By letting a driver upload information into their app, it makes it easier for them to process the information in sorting centers and fulfillment centers further down the flow; some apps can even reroute orders that were originally on different runs. Drivers should be able to scan specific products from a single order as well.
A reverse logistics process occurs for many reasons. Reverse logistics processes are used to manage failed deliveries, damages during transport, and compliance with the law. For example, an app called Driver App helps retailers track driver returns to minimize lost sales revenue. The five common use cases of reverse logistics include customer returns, failed deliveries (from drivers), returning damaged parts or products that were returned by customers, waste management and disposal (of goods delivered back), and recycling (in some industries).
The use of driver apps to manage failed delivery attempts, damaged goods, and compliance can help reduce the stress associated with distribution. Driver apps offer a hybrid flow that includes both pickups and drop-offs.
Reverse logistics returns processing
Reverse logistics refers to the return of goods. Reverse logistics is becoming more important with the growing success of online shopping and digital supply chains. Customers should be able to request returns, receive printable barcodes, and schedule them from retailers’ websites or apps. UPS offers a portfolio of returns management services for businesses that need assistance with reverse logistics processes.
Reverse logistics is the process of returning goods to their original manufacturer or supplier. UPS helps grow companies by providing reverse logistics services, which include distribution, warehouse fulfillment, and repairs.
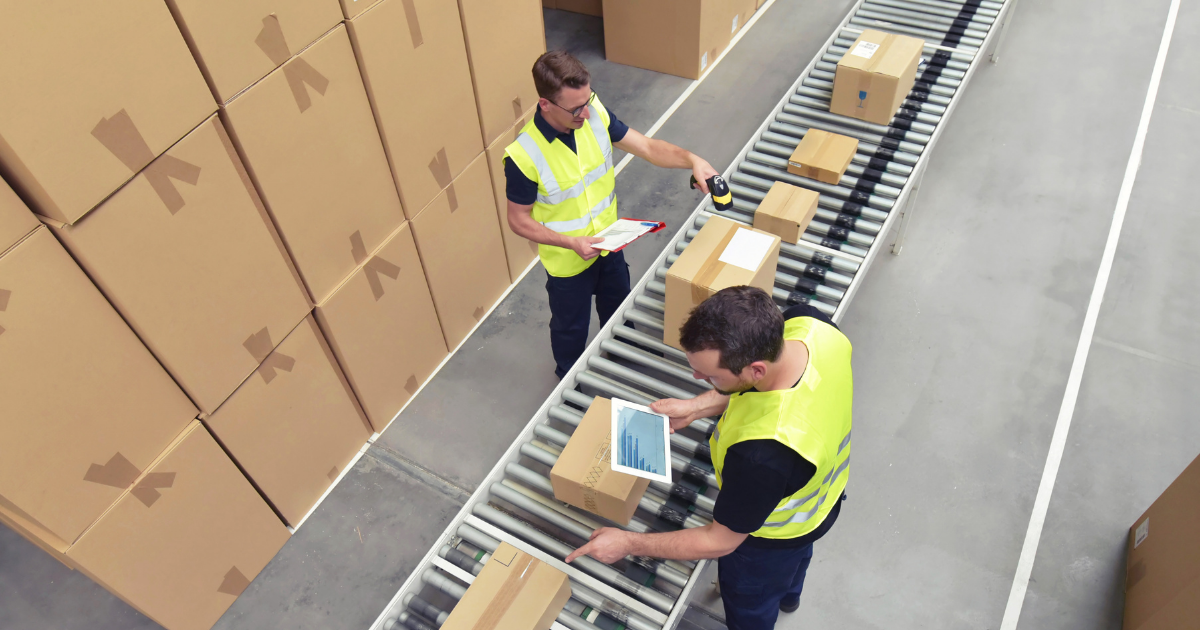
Connecting your systems
Reverse logistics is the process of taking an item that has been sent to be recycled and reusing materials from it. Reverse logistic systems should integrate with other supply chain management software such as inventory management, POS, WMS, or IMS. Inventory scanning at a sorting center would then provide visibility across the entire supply chain.
The first step to reverse logistics is digitizing and automating the process. This allows a company to handle a massive amount of goods with traditional logistics not being able to carry them all.
Treat the return experience as you would any other
Reverse logistics is a strategy in which companies take the initiative in managing the return process for their products. This includes sending notifications to customers when drivers have picked up the product, sending a message with a link to reschedule a delivery, and providing transparency throughout the reverse supply chain.
The return experience is considered a necessary evil for retailers. However, it is still important to consider the benefits that come with reducing costs or restoring customers’ faith in your brand.
There are many opportunities for entrepreneurs to turn a mistake into an unplanned profit. Treat the return experience as you would any other and take advantage of what happens after the product has been tagged for outbound logistics.
In order to treat the return experience as you would any other, companies should have a good reverse logistics program in place. This will allow customers who are returning items to get their money back and provide them with an excellent customer service experience.
Use packaging as return labels to reduce return rates
Reverse logistics is the process of providing customers with the product without having to carry it all the way back to the supplier. UPS has a range of services that can help improve customer satisfaction and reverse logistics management as well as distribution, warehousing fulfillment, and repairs. Scaling up with less capital investment is easier for businesses using these services like UPS, which builds customer loyalty leading to increased revenue for companies.
Reverse logistics is the process of processing returned goods to recover them for reuse. Online marketplaces have return policies that allow sellers to disclose this information and document their returns so fraudulent claims can be avoided. Reverse logistics is a necessary tool to reduce high return rates, which would otherwise lead retailers into financial loss and reduced profits.
Retailers should use packaging to reduce the exposure of product returns. By doing this, retailers can identify where customers are experiencing high return rates and take corrective actions accordingly.
Create a returns policy that meets customer demand and protects your profits
Reverse logistics refers to the process of handling products that have been delivered to a business. This can be done through various methods, such as returns management solutions and UPS post-sales services. Companies should consider creating a return policy that meets customer demand and protects their profits.
Today, the customer is in control. When you create a returns policy that meets your customers’ demands and protects your profits, it keeps them happy and engaged with your company.
Save money with help from a reverse logistics expert
Reverse logistics is a strategy that aims to reduce risk, maximize the value of assets, and collaborate with supply chain experts. Reverse logistics can be achieved by utilizing high-capacity networks at the local, regional, national, and international levels. Reverse logistics programs are most effective when they are well-planned in advance.
Having an expert to help you out with reverse logistics is a good way to save money. A company like C.H Robinson Navisphere® can help make your supply chain more efficient, increasing visibility through technology such as the Computerized Handling System (CH) and Global Logistics Providers (GLP).
Quickly assess the condition of the returned product
Reverse logistics is the process of collecting, storing, and analyzing customer returns. This helps companies stay competitive by understanding their customers better.
Quickly assessing the condition of the returned products is important for minimizing costs associated with reverse logistics. Managing your own reverse logistics will take attention away from growing your business, so it’s best to hire a third-party company for this service.
Use return logistics data to improve product design
Reverse logistics is about managing return shipments to improve product design and reduce the cost of inventory. Reverse logistics has been a trend for SCM and e-commerce technologies such as barcodes, scanners, and EDI. Blockchain is the latest trend in reverse logistics related to tracking returns, materials handling systems in warehouses, and more.
- 10 Facts About Supply Chain Analysts Skills You Need to Know About - April 24, 2023
- What Are The Most Common Shipping Mistakes and How to Avoid Them - December 8, 2021
- What is “Reverse Logistics” and How Can You Benefit From It? - November 24, 2021